Optimizing Industrial External Logistics with Griffin Tracker
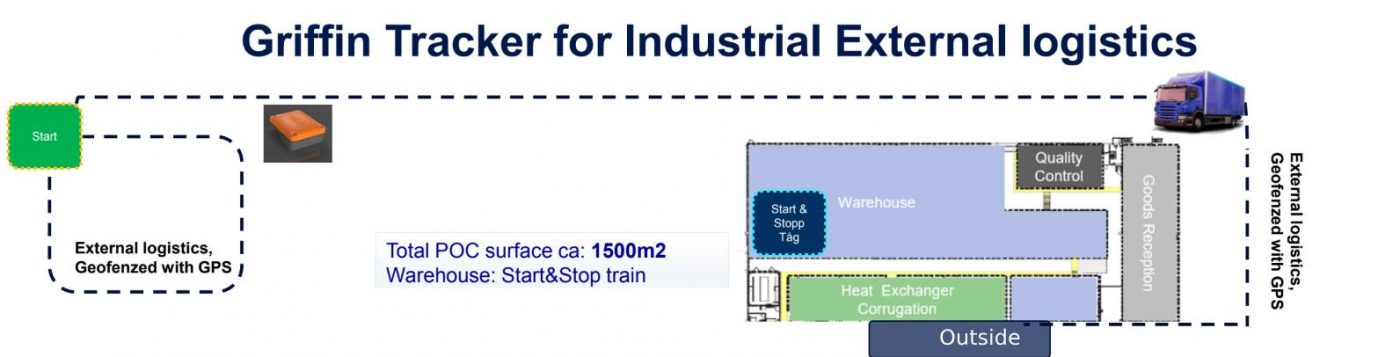
Customer Case Study: Optimizing Industrial External Logistics with Griffin Tracker
A leading global company in the food processing and packaging industry, with a vast network of factories and suppliers worldwide, sought to enhance its external logistics operations at one of its key production centers in Sweden. The facility, a hub for research, development, and production, managed a 1,500 m² proof-of-concept (POC) area that included a warehouse with start-and-stop train systems and external logistics zones. The company faced challenges in tracking assets like pallets and transport equipment, which led to inefficiencies such as misplaced items, delays, and increased operational costs. These issues disrupted the seamless flow of materials essential for the production of packaging and processing systems, impacting overall efficiency.
To tackle these challenges, the company collaborated with H&D Wireless to implement the Griffin Tracker for Industrial External Logistics, a geofenced GPS solution powered by the Raven IoT sensor. The deployment took place during a significant POC in Q1-Q2 2021, aligning with the company’s strategic goals for 2030, which prioritized sustainability and operational efficiency. The Raven IoT sensor, equipped with GPS L1 C/A, LTE-M, and NB-IoT communication technologies, enabled real-time tracking and geofencing of assets across the 1,500 m² area. Integrated with the Griffin IoT Cloud, the solution provided a comprehensive overview of asset locations and movements, eliminating the need for local infrastructure like Wi-Fi or Bluetooth and ensuring seamless data flow.
Tetra Pak has identified HDW's technology as priority for 2 of 3 goals for 2030.
The Griffin Tracker significantly improved the company’s external logistics operations. By implementing geofencing, the solution ensured that assets, such as pallets used for transporting packaging materials, remained within designated zones, drastically reducing the risk of misplacement. In a typical industrial logistics environment, misplaced assets can cause delays costing hundreds of dollars per incident. The Griffin Tracker minimized these occurrences, ensuring each pallet was readily available for production needs. Industry benchmarks indicate that real-time tracking solutions can reduce asset misplacement by up to 25%. For a single pallet, this translates to avoiding approximately one misplacement incident per month. At an estimated cost of $200 per incident (accounting for labor and downtime), this results in savings of $200 per pallet per month, or $2,400 annually per unit.
The solution also enhanced the efficiency of the warehouse’s start-and-stop train system, which is critical for material flow. By providing real-time visibility into the location and status of transport equipment, the Griffin Tracker reduced idle time and ensured timely delivery of materials to production lines. This optimization decreased handling time by an estimated 10 minutes per pallet movement. With labor costs in a high-tech facility averaging $40 per hour, this 10-minute saving per pallet equates to $6.67 per movement. For a single pallet moved 10 times daily, this results in a daily labor cost saving of $66.70, or approximately $16,000 annually per pallet, directly attributable to improved logistics efficiency.
Furthermore, the Raven IoT sensor’s environmental monitoring capabilities—featuring temperature, accelerometer, and magnetic field sensors—enabled the company to monitor the condition of transport equipment like the start-and-stop trains, ensuring optimal performance. This proactive monitoring reduced equipment failures and minimized downtime. Industry studies show that IoT-enabled monitoring can reduce equipment downtime by 15–20%. For a single train system, this translates to avoiding around 1 hour of downtime per month. At an estimated downtime cost of $3,000 per hour in a high-volume production center, this equates to savings of $3,000 per train per month, or $36,000 annually per unit.
The success of the 2021 POC highlighted the transformative potential of IoT-driven logistics solutions. The Griffin Tracker not only delivered direct cost savings but also supported the company’s broader sustainability and efficiency goals by reducing resource waste and enhancing supply chain visibility. Its seamless integration with the Griffin IoT Cloud, along with compatibility with standard cloud platforms like Microsoft Azure, made it a flexible and scalable solution for the company’s global operations.