Raven BOX827 – Industrial Telpher
Customer Case Study: Enhancing Industrial Assembly with Raven BOX827 IoT Solution
A leading manufacturer of heavy transport vehicles, operating a highly automated production facility in Sweden, faced significant challenges in maintaining the uptime of critical equipment used in its assembly processes. The facility needed to move and assemble over 10,000 objects daily, including 200 engine blocks, to meet its production quota. The equipment in question—industrial telphers—was essential for handling these components, but any downtime risked halting the assembly line, leading to delays, increased labor costs, and potential penalties for missing production targets. Additionally, the lack of real-time visibility into equipment health resulted in reactive maintenance practices, causing unexpected failures and inefficient resource allocation.
To address these issues, the company collaborated with H&D Wireless to implement the Raven BOX827 IoT sensor solution, a cutting-edge tool designed for condition-based maintenance and real-time equipment monitoring. The Raven BOX827 was installed on each industrial telpher, leveraging its environmental sensors—temperature, accelerometer for vibrations, and magnetic field/EMC—to continuously monitor equipment health. Integrated with the Griffin IoT Cloud, the solution provided a seamless, real-time data overview, enabling predictive maintenance and automated alerts for potential issues. The use of LTE-M and NB-IoT cellular standards eliminated the need for local infrastructure like Wi-Fi or Bluetooth, ensuring a quick and cost-effective deployment.
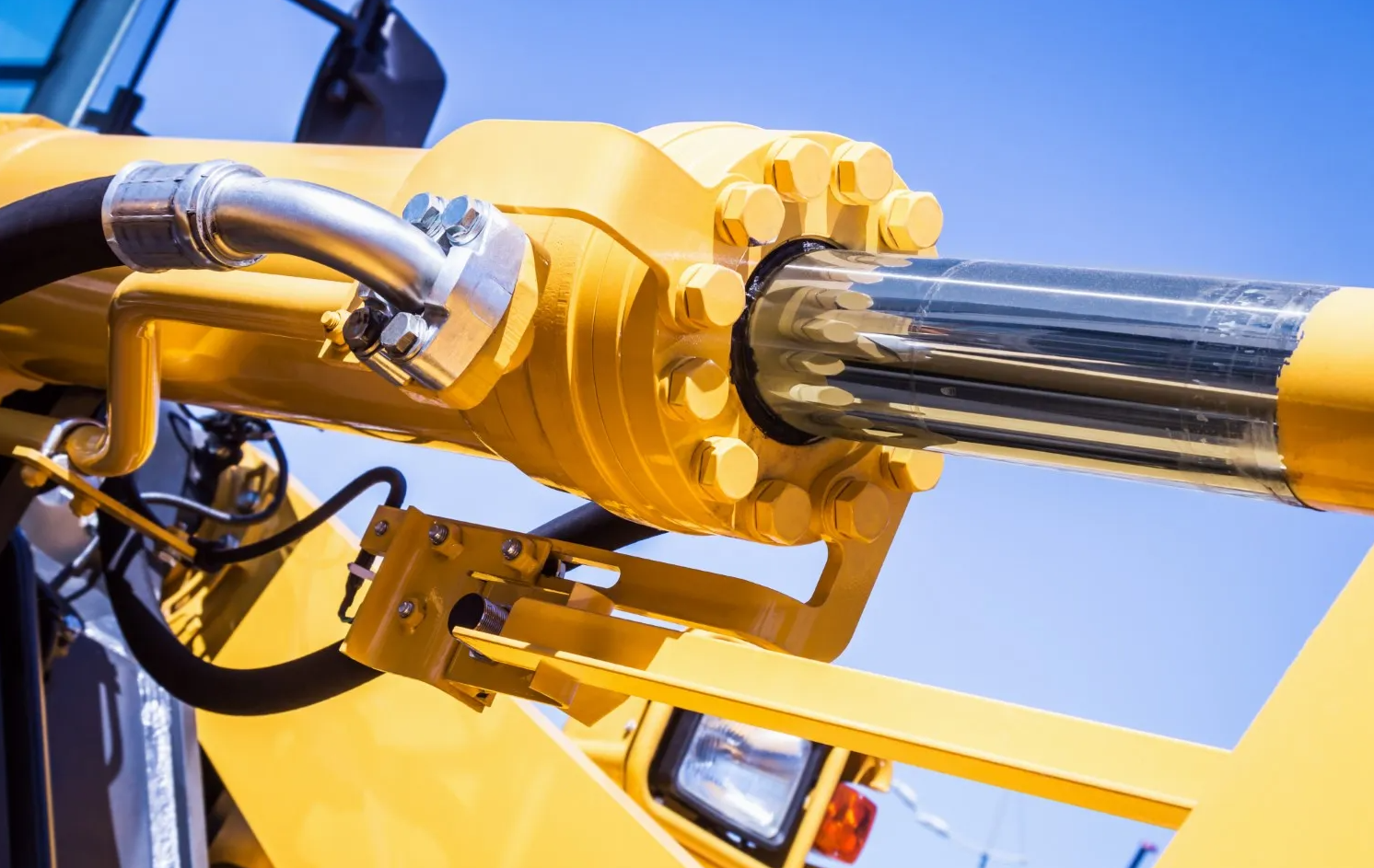
The Raven BOX827 delivered transformative results for the company’s operations. By monitoring vibrations and temperature, the solution detected early signs of wear in telpher components, such as motors and lifting mechanisms, allowing for proactive maintenance scheduling. This predictive approach significantly reduced unexpected downtime. In a typical industrial setting, unplanned downtime can cost manufacturers thousands of dollars per hour. The Raven BOX827 ensured that each telpher, critical for moving components to assemble 200 engine blocks daily, remained operational. Industry benchmarks indicate that predictive maintenance solutions can reduce downtime by up to 30%. For a single telpher, this translates to avoiding approximately 2 hours of downtime per month. At an estimated downtime cost of $5,000 per hour for a high-volume assembly line, this equates to savings of $10,000 per telpher per month—or $120,000 annually per unit.
The solution also enhanced
workflow efficiency by tracking and locating assets within cellular coverage, ensuring telphers were optimally positioned to reduce idle time. The digital visualizer in the Griffin IoT Cloud provided actionable insights, such as usage patterns and health status, further optimizing maintenance schedules and reducing service management fees. Industry studies suggest that IoT-enabled predictive maintenance can cut maintenance costs by 10–20%. For the company, this meant saving approximately 15% on maintenance costs per telpher. With an annual maintenance cost of around $8,000 per telpher, this results in savings of $1,200 per telpher per year.
Production efficiency saw significant improvements as well. By ensuring telphers remained operational, the company maintained its quota of assembling 200 engine blocks daily without delays. The Raven BOX827’s automated alarms and notifications enabled technicians to address issues before they escalated, minimizing disruptions. For each engine block, the seamless operation of telphers reduced handling time by an estimated 5 minutes per block due to optimized positioning and fewer equipment failures. With labor costs in a high-tech assembly plant averaging $50 per hour, this 5-minute saving per block equates to approximately $4.17 per engine block. For 200 engine blocks daily, this results in a daily labor cost saving of $834, or over $200,000 annually, directly attributable to improved telpher efficiency.
Beyond these financial benefits, the Raven BOX827 integrated seamlessly with the company’s existing asset management systems via Griffin cloud-based APIs, streamlining data flow and enhancing decision-making. The real-time insights also supported the company’s broader digital transformation goals, aligning with its initiatives to adopt Industry 4.0 technologies, a focus it has pursued since collaborating with H&D Wireless in 2017. This not only boosted operational efficiency but also positioned the company as a leader in smart manufacturing.
This case study highlights the potential of IoT solutions for manufacturers facing similar challenges, such as equipment downtime, inefficient maintenance, or lack of visibility into asset performance. The per-unit savings achieved—such as $120,000 annually in downtime avoidance and $1,200 in maintenance cost reductions per telpher—demonstrate the scalability of this solution across fleets of any size. Additionally, its compatibility with cloud platforms like Microsoft Azure or Amazon Web Services ensures adaptability to various operational environments. For manufacturers aiming to remain competitive in a rapidly evolving industry, investing in IoT-enabled predictive maintenance offers not only cost savings but also a strategic path toward smarter, more resilient operations. This experience underscores the future of manufacturing as a connected, data-driven landscape, encouraging others to adopt similar technologies.
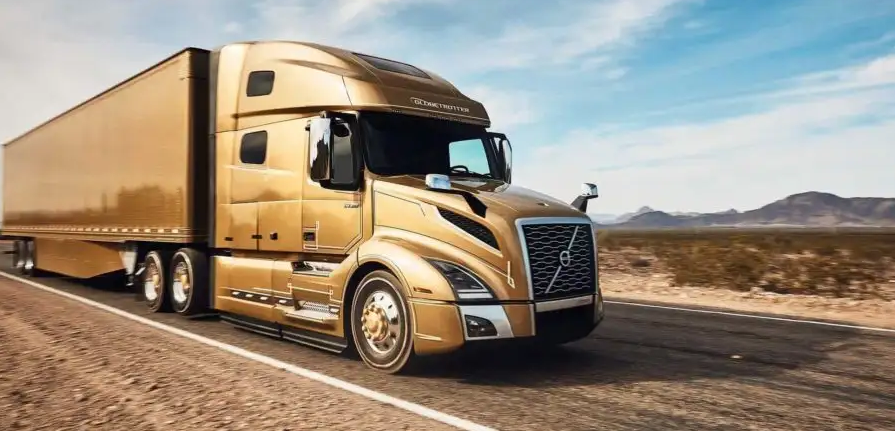